- Joined
- Sep 1, 2012
- Messages
- 46
It seems to me that most mods are aimed at aesthetic improvement to games and whilst there’s nothing wrong with that (when done tastefully of course
), I wondered how many of you have made mods to overcome actual / perceived design flaws in games. I’m thinking along the lines of the extended outlane ball guides on STTNG or the reinforced slot machine target for TZ.
By way of example, here’s something I recently created for my Gottlieb Freddy. The design flaw is with the boiler door mechanism as when it is in the up position there is only a small gap between the top of the door and the door frame. The designers presumably thought that the chance of a ball having just the right momentum to balance on the door as it rises and get stuck between the top of the door and the frame were too remote to worry about. Turns out they were wrong – it happens more often than physics suggests it should!
When this happens, it forces the motor to try to squash the ball between the door and door frame. This obviously won’t happen so instead it stresses the motor mech and results in the actuator arm being forced into the wrong position and so the door will no longer fully close. Over time, it could break the motor mechanism or boiler door.
Strictly speaking, this makes the game easier as the door spends more time in its flat position making it easier to get a ball into the boiler but, being a touch OCD, I can’t leave it like that without it greatly annoying me and I have to head under the playfield to reset it.
I decided to come up a solution to the problem and settled on a spring-loaded platform that would sit in-between the actuator arm and the bottom of the boiler door. A spring-loaded actuator arm may have been easier but this way it can easily be removed if someone wants to go back to factory original.
3D printing seemed to be the way to go so I checked with @myPinballs what format he’d need if I wanted something printing (.stl being the answer) and then found a suitable free CAD program to design it – I went with Tinkercad.
It took 2 attempts – the first worked but there were areas for improvement. The final design looks like this in Tinkercad.
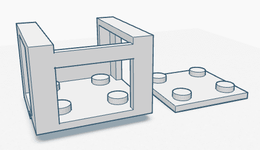
Fully assembled with the 4 springs it looks like this:
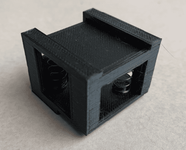
I then just added some 3M double sided tape (the type used for siderails) and aligned it so that the actuator strikes in the middle to balance the load between the 4 springs.
The attached 2 short videos show the mech being cushioned by the spring-loaded platform when encountering resistance and the boiler door coping with a ball trap.
Rather pleased with the result and special mention goes to Jim @myPinballs for his expert 3D printing – highly recommended!
So, anyone else got any DIY improvements they’ve made to games to fix design issues?

By way of example, here’s something I recently created for my Gottlieb Freddy. The design flaw is with the boiler door mechanism as when it is in the up position there is only a small gap between the top of the door and the door frame. The designers presumably thought that the chance of a ball having just the right momentum to balance on the door as it rises and get stuck between the top of the door and the frame were too remote to worry about. Turns out they were wrong – it happens more often than physics suggests it should!
When this happens, it forces the motor to try to squash the ball between the door and door frame. This obviously won’t happen so instead it stresses the motor mech and results in the actuator arm being forced into the wrong position and so the door will no longer fully close. Over time, it could break the motor mechanism or boiler door.
Strictly speaking, this makes the game easier as the door spends more time in its flat position making it easier to get a ball into the boiler but, being a touch OCD, I can’t leave it like that without it greatly annoying me and I have to head under the playfield to reset it.
I decided to come up a solution to the problem and settled on a spring-loaded platform that would sit in-between the actuator arm and the bottom of the boiler door. A spring-loaded actuator arm may have been easier but this way it can easily be removed if someone wants to go back to factory original.
3D printing seemed to be the way to go so I checked with @myPinballs what format he’d need if I wanted something printing (.stl being the answer) and then found a suitable free CAD program to design it – I went with Tinkercad.
It took 2 attempts – the first worked but there were areas for improvement. The final design looks like this in Tinkercad.
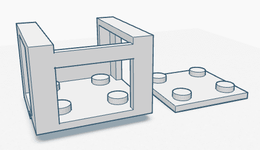
Fully assembled with the 4 springs it looks like this:
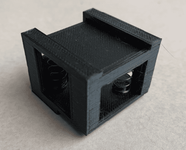
I then just added some 3M double sided tape (the type used for siderails) and aligned it so that the actuator strikes in the middle to balance the load between the 4 springs.
The attached 2 short videos show the mech being cushioned by the spring-loaded platform when encountering resistance and the boiler door coping with a ball trap.
Rather pleased with the result and special mention goes to Jim @myPinballs for his expert 3D printing – highly recommended!

So, anyone else got any DIY improvements they’ve made to games to fix design issues?