Ello,
I rebuilt my friends Funhouse flipper last night after the EOS switch blade had snapped off and as a result blew the flipper fuse. I started at about 7:30pm, and finished about three hours later.
What I've realised very quickly is that my soldering skills are useless. I bought a lithium battery powered soldering iron a while back, and whilst it was ok it didn't seem to be able to melt the solder that was already on the wires attached to the coil lugs when I attempted to desolder them. I ended up breaking out a mains powered one, which fared a bit better.
I had no problems taking the mechanism off the machine and taking it apart, putting it back together with new parts, but I really struggled with the soldering and desoldering aspect. When soldering I just seemed to get solder on the tip of the iron when offering up the solder reel to it, or I just ended up with a charred mess. I didn't even seem to be able to tin the wires properly, I don't know if that's because they had residual solder on them or not?
I also managed to burn my hand more than once. I felt pretty useless by the end of it. I've watched videos where people just pretty much glide over the lugs and wires and get a perfect, smooth solder blob on them. It felt like surgery for me.
This was the end result... not a pretty picture but the wires are at least attached well enough that you can wiggle them, etc. I don't know if it actually works yet because I'm waiting on a delivery of 2.5A SB fuses.
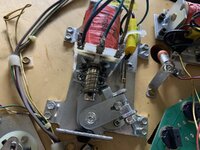
Anyone care to share any tips or links to equipment they use?
I rebuilt my friends Funhouse flipper last night after the EOS switch blade had snapped off and as a result blew the flipper fuse. I started at about 7:30pm, and finished about three hours later.

What I've realised very quickly is that my soldering skills are useless. I bought a lithium battery powered soldering iron a while back, and whilst it was ok it didn't seem to be able to melt the solder that was already on the wires attached to the coil lugs when I attempted to desolder them. I ended up breaking out a mains powered one, which fared a bit better.
I had no problems taking the mechanism off the machine and taking it apart, putting it back together with new parts, but I really struggled with the soldering and desoldering aspect. When soldering I just seemed to get solder on the tip of the iron when offering up the solder reel to it, or I just ended up with a charred mess. I didn't even seem to be able to tin the wires properly, I don't know if that's because they had residual solder on them or not?
I also managed to burn my hand more than once. I felt pretty useless by the end of it. I've watched videos where people just pretty much glide over the lugs and wires and get a perfect, smooth solder blob on them. It felt like surgery for me.
This was the end result... not a pretty picture but the wires are at least attached well enough that you can wiggle them, etc. I don't know if it actually works yet because I'm waiting on a delivery of 2.5A SB fuses.
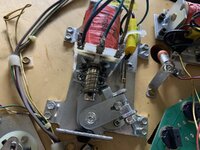
Anyone care to share any tips or links to equipment they use?